Mastering the Art of Screenprinting Ink: A Comprehensive Guide
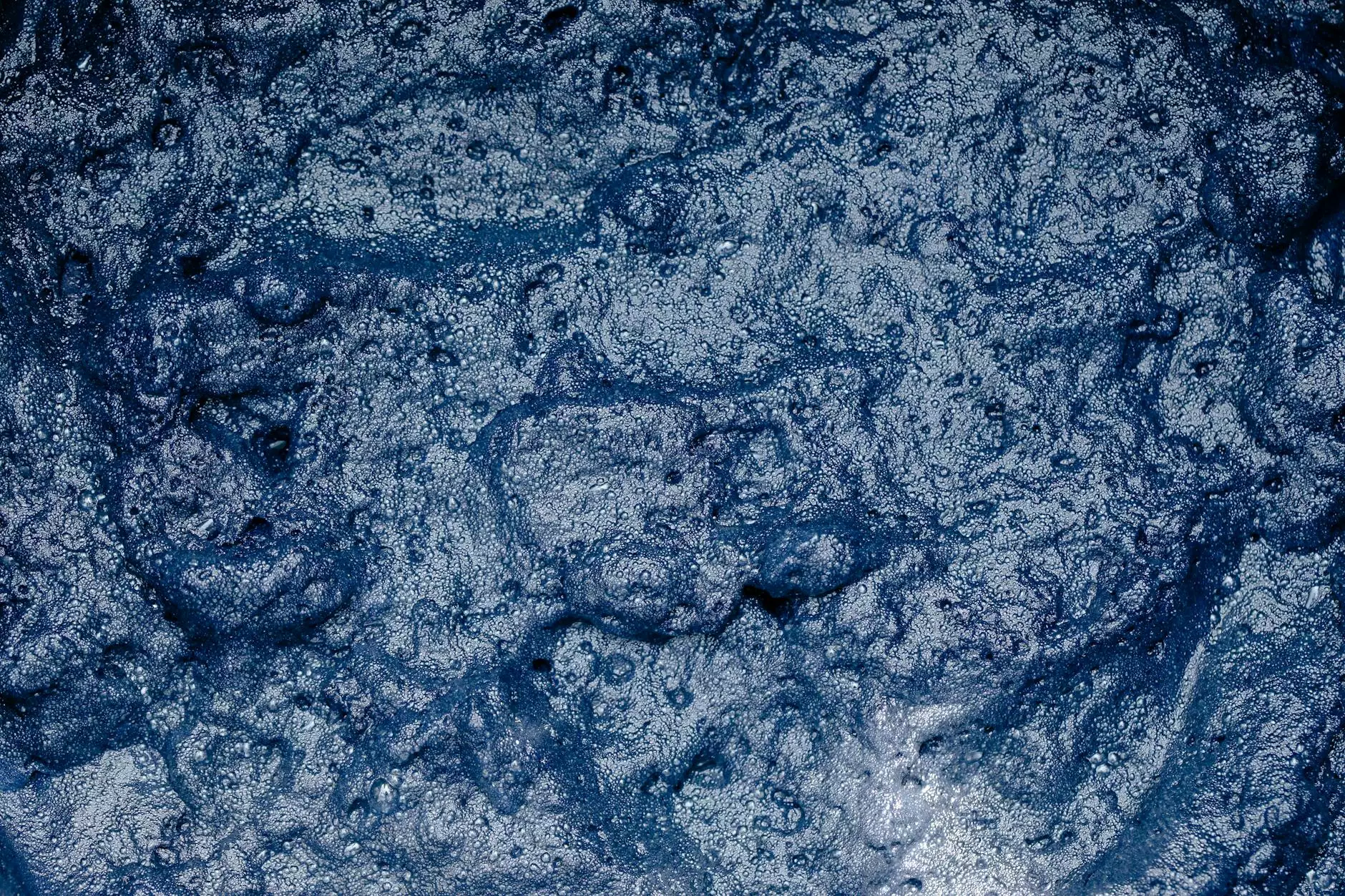
In the realm of printing services, few elements are as critical as the quality of screenprinting ink. The right ink can make the difference between a lackluster print and a vibrant masterpiece. At Boston Industrial Solutions, we understand the significance of premium inks in delivering exceptional results. This article delves deeply into the world of screenprinting ink, exploring its types, applications, and best practices.
The Importance of Choosing the Right Screenprinting Ink
Choosing the right screenprinting ink is essential to achieving the desired outcome in any printing project. Here are several reasons why:
- Vibrancy and Color Fastness: High-quality inks yield brighter colors and ensure that prints stay vibrant over time.
- Durability: Certain inks are designed to withstand environmental challenges, making them ideal for outdoor applications.
- Adhesion: Quality inks interfere less with substrate surfaces, providing better adhesion and longevity of the print.
- Special Effects: Specialty inks, such as metallic or glow-in-the-dark, can add unique effects to your prints.
Types of Screenprinting Ink
Understanding the different types of screenprinting ink available on the market is crucial for selecting the right one for your project. Below are the primary types:
1. Plastisol Ink
This is perhaps the most popular choice in the screenprinting industry. Plastisol ink is known for its vibrant colors and exceptional opacity, which is suitable for a wide array of fabrics. It does not dry until it is cured with heat, allowing for great workability.
2. Water-Based Ink
Water-based inks are preferred for their eco-friendliness. They penetrate the fabric, resulting in a softer hand feel. However, they require careful handling to avoid premature drying on screens.
3. Discharge Ink
Discharge ink is unique as it removes the dye from the fabric while leaving the original color. This type of ink is highly praised for its ability to produce pastel colors on dark fabrics.
4. Specialty Inks
These include inks that offer unique finishes, such as metallic, fluorescent, or glow-in-the-dark properties, adding visual intrigue to your prints.
Application of Screenprinting Ink
The application of screenprinting ink is a nuanced process that influences the outcome of the printed material. Below are steps to ensure successful application:
1. Screen Preparation
Before printing, it is critical to prepare your screen. This involves cleaning the screen thoroughly and ensuring that emulsion layers are correctly applied to prevent ink bleed.
2. Ink Mixing
Depending on your project, you may need to mix inks to achieve the desired color. Always follow the manufacturer's guidelines to maintain consistency.
3. Printing Techniques
Utilize proper printing techniques, such as different stenciling methods or screen mesh selections, to optimize the transfer of the screenprinting ink.
4. Curing the Ink
Proper curing is essential for durability. Each type of ink has specific curing requirements, often at designated temperature levels.
Common Problems and Solutions in Screenprinting Ink
Despite careful execution, various challenges may arise when working with screenprinting ink. Understanding these problems allows for effective troubleshooting:
1. Ink Bleeding
Ink bleeding can occur due to improper emulsion application or using too much ink. Ensuring that your screen is clean and not overloaded with ink can mitigate this issue.
2. Inconsistent Color
Mixing different batch inks can lead to color inconsistencies. Always ensure that you use inks from the same batch whenever possible.
3. Curing Issues
If prints are not cured correctly, they can wash out easily. Always follow the manufacturer's guidelines for duration and temperature settings during curing.
Eco-Friendly Screenprinting Ink: The Future of Printing Services
As sustainability becomes more crucial in the printing industry, the demand for eco-friendly screenprinting ink continues to grow. Water-based inks and soy-based inks are becoming increasingly popular alternatives. They offer various advantages:
- Reduced Toxicity: These inks contain fewer harmful chemicals, ensuring a safer working environment.
- Biodegradability: Eco-friendly inks are often biodegradable, which reduces their environmental impact.
- Consumer Demand: Many consumers prefer products made with sustainable practices, making eco-friendly inks a great selling point.
Conclusion
In conclusion, mastering screenprinting ink is fundamental for anyone involved in printing services. From understanding the types of inks available to navigating the application process, each aspect plays a pivotal role in achieving high-quality prints. At Boston Industrial Solutions, we are dedicated to providing top-notch inks and resources to ensure your projects are nothing short of perfection. By prioritizing quality and sustainability in your choice of printing materials, you will not only meet client demands but elevate your brand's reputation in the printing industry. Explore our range of screenprinting inks and discover the difference that quality makes.